1. Đặt vấn đề
Quá trình sản xuất clinker và xi măng đã thải ra môi trường một lượng nhiệt khá lớn, gây lãng phí năng lượng và ô nhiễm môi trường. Hiện nay, mặc dù công nghệ sản xuất xi măng đã được cải tiến để giảm thiểu đến mức tối đa lượng nhiệt lãng phí, tuy nhiên, vẫn còn đáng kể một lượng nhiệt tổn thất ra ngoài môi trường.
Trên cả nước, tình trạng thiếu điện vẫn thường xảy ra, do đó vấn đề tiết kiệm điện và sử dụng nguồn nhiệt thừa để phát điện là cấp bách. Theo tính toán, với 1 tấn khí thải có thể sản xuất ra 3 – 4 kWh điện. Như vậy, với lượng nhiệt đang thải ra từ các nhà máy xi măng nếu được tận dụng sẽ giúp tạo ra một lượng điện năng đáng kể để quay lại phục vụ quá trình sản xuất.
2. Cơ cấu tiêu thụ năng lượng trong nhà máy xi măng
Sản xuất xi măng sử dụng khá nhiều năng lượng, năng lượng cần thiết thường ở 2 dạng chính:
– Năng lượng nhiệt (than): Sử dụng chủ yếu cho lò nung clinker và calciner.
– Năng lượng điện: Cung cấp cho hệ thống thiết bị sản xuất (máy nghiền liệu, nghiền xi măng…), phụ trợ (khí nén, bơm nước,…), chiếu sáng, văn phòng,… (Bảng 1)
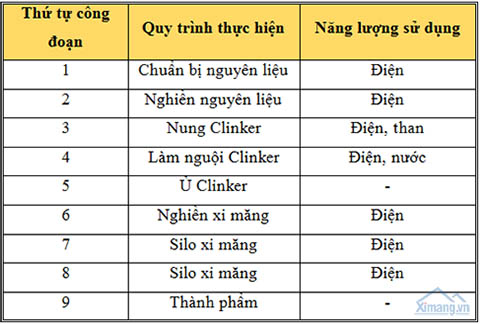
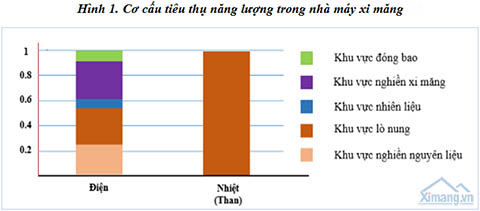
Để nghiên cứu khả năng ứng dụng đồng phát điện trong nhà máy xi măng, tác giả đã tiến hành thu thập số liệu về tiêu thụ năng lượng và phát thải nhiệt tại một nhà máy xi măng ở Việt Nam với 2 dây chuyền sản xuất. Các thông số cơ bản thu thập từ nhà máy này sẽ được sử dụng để tính toán các chỉ số kinh tế – kỹ thuật khi ứng dụng công nghệ đồng phát.
3.1. Cơ cấu năng lượng tiêu thụ
Với 2 dây chuyền sản xuất xi măng của nhà máy, lượng điện năng tiêu thụ một năm của toàn nhà máy khoảng 261.772.776 (kWh) – tương đương 40.962 TOE, và tiêu thụ khoảng 380.026 (tấn) than – tương đương 246.181 TOE. (Hình 2)
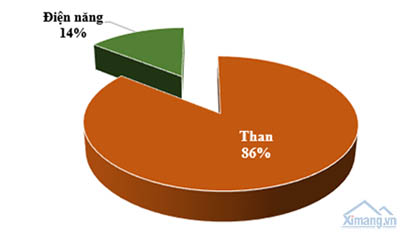
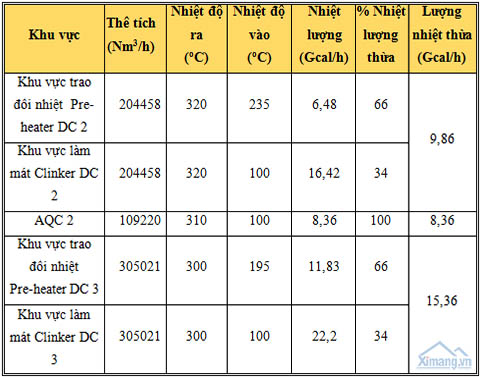
4.1. Phân tích về kỹ thuật
Để tận dụng nhiệt thừa từ quá trình sản xuất xi măng, nghiên cứu sẽ tiến hành tận dụng nhiệt thừa tại:
– Nhiệt thải từ hệ thống làm mát clinker dây chuyền thứ nhất;
– Nhiệt thải từ hệ thống tháp gia nhiệt dây chuyền thứ nhất và dây chuyền thứ hai.
Với nhiệt độ khói thải từ khoảng 300 – 330oC, tổng lượng nhiệt dư thừa từ hệ thống làm mát clinker dây chuyền thứ nhất, hệ thống tháp gia nhiệt dây chuyền thứ nhất và dây chuyền thứ 2 vào khoảng 33,67 (Gcal/h). Có hai phương án lựa chọn tuabin cho sản xuất điện: Một là sử dụng hơi nước; Hai là sử dụng dung môi. Với từng phương án, khả năng phát điện từ việc thu hồi nhiệt thải được đưa ra trong Bảng 3.
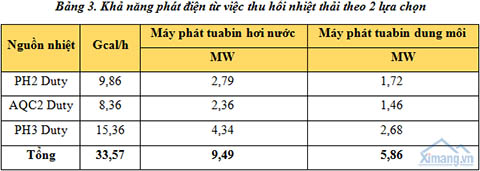
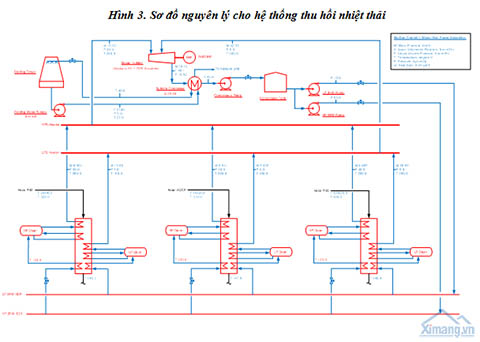
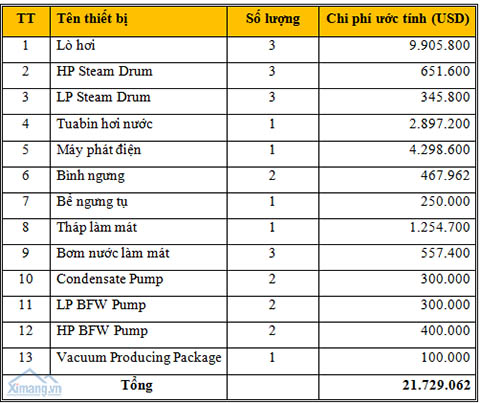
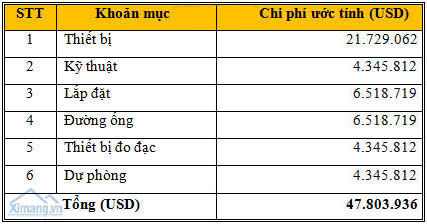
– Thời gian vòng đời dự án: 30 năm.
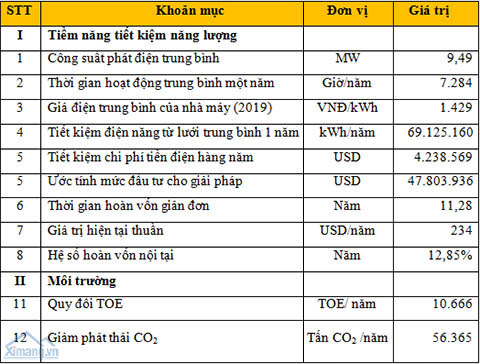
Với hiện trạng cụ thể của nhà máy, công suất phát điện trung bình đạt 9,49 MW. Với thời gian hoạt động trung bình trong một năm là 7.284 giờ/năm, hệ thống phát điện sẽ sản xuất 69.125.160 kWh/năm. Cũng có thể hiểu, khi nhà máy áp dụng giải pháp tận dụng nhiệt thải để phát điện, hàng năm sẽ tiết kiệm được 69.125.160 kWh từ lưới.
– Về kinh tế:
• Thời gian hoàn vốn của dự án: 11,28 năm;
• Tiết kiệm chi phí tiền điện hàng năm: 4.238.569 USD/năm;
• Ước tính mức đầu tư cho giải pháp: 47.803.936 USD;
• Giá trị hiện tại thuần NPV: 234 USD/năm;
• Hệ số hoàn vốn nội tại IRR: 12,85%.
Từ (1) (2) (3): Kết luận giải pháp khả thi về mặt kinh tế.
Căn cứ vào tính khả thi về mặt kỹ thuật và kinh tế, kết luận: Giải pháp thu hồi nhiệt thải để phát điện khả thi về mặt kỹ thuật – kinh tế.
5. Kết luận
Các phân tích cho thấy, khả năng tận dụng lượng nhiệt thừa trong nhà máy sản xuất xi măng là khá lớn. Điều này có thể áp dụng để giúp các nhà máy sử dụng hiệu quả năng lượng, góp phần bảo vệ môi trường và giảm bớt gánh nặng cho các doanh nghiệp điện sử dụng các nguồn nhiên liệu truyền thống.